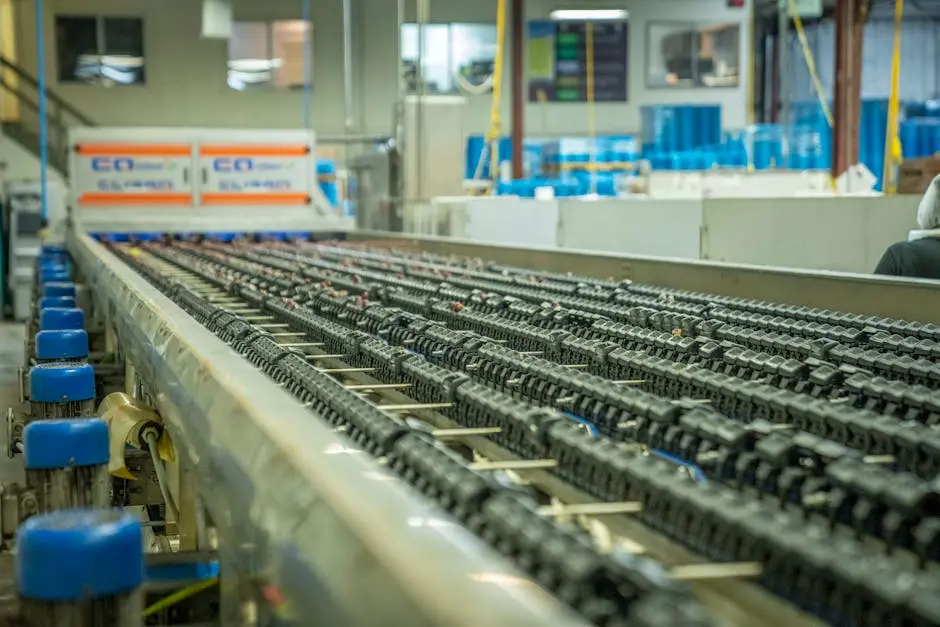
Foam gasket material is increasingly becoming a popular choice for a variety of industrial applications due to its versatility and reliability. As a leading industrial gasket solution, it offers unique properties that make it ideal for a wide range of uses, including sealing, insulation, and vibration dampening. Its adaptability and performance make flexible foam gaskets the go-to choice for industries ranging from automotive and HVAC to electronics and construction. In this guide, we will explore the many reasons why foam gasket material stands out as a superior option in industrial settings, offering efficiency, durability, and customised solutions to meet diverse requirements.
Understanding Foam Gasket Material
Foam gasket material is primarily composed of a variety of polymers, which gives it distinct advantages over traditional gasket materials. This flexibility allows it to conform to various surfaces, creating a reliable seal that prevents the ingress of air, moisture, and contaminants.
One of the most compelling aspects of foam gasket material is its lightweight nature. Unlike heavier materials, foam gaskets can be easily handled and installed, making them particularly advantageous for large-scale applications where weight can be a concern.
In addition to being lightweight, foam gasket materials also boast a high resistance to various chemicals and temperatures. This quality ensures their longevity, making them a cost-effective choice for industrial environments that face challenging conditions.
Benefits of Foam Gasket Material
There are several benefits to using foam gasket material in industrial applications. First and foremost, its compressibility allows for effective sealing even on uneven surfaces. This ensures that a tight seal is achieved, protecting against leaks and enhancing efficiency.
For those concerned about energy efficiency, foam gasket material is a game-changer. Its insulating properties help reduce energy loss, translating to lower operating costs. Industries focused on sustainability can particularly benefit from incorporating this type of gasket.
Another significant benefit is the ease of installation. Foam gasket material can be cut to size, and many varieties come with adhesive backing that simplifies the application process. This reduces downtime and labor costs, making it an optimal choice for busy industrial settings.
Applications in Industrial Settings
Foam gasket materials are versatile, finding application across multiple industries. For example, in the automotive sector, they are used to seal doors, windows, and hoods, ensuring effective sound dampening and thermal insulation. This enhances comfort while reducing noise vibrations.
In the HVAC industry, foam gaskets play a critical role in sealing ductwork. By preventing air leakage, they promote better airflow and increase overall system efficiency. This application is crucial, especially in environments where energy conservation is a priority.
Additionally, foam gaskets are prevalent in manufacturing settings, often used to provide cushioning and protection for components during assembly. This reduces wear and tear, ultimately extending the lifespan of machinery and equipment.
Comparing Gasket Material to Other Types
When comparing foam gasket material to traditional rubber or cork gaskets, the advantages quickly become apparent. Foam gaskets maintain flexibility over a wide temperature range, while rubber can harden or degrade, leading to ineffective seals over time.
Moreover, unlike cork, which tends to absorb moisture and can swell, foam gaskets remain unaffected by water and most chemicals, reinforcing their reliability in various industrial applications. This makes foam gaskets a preferred choice for sealing in moist or corrosive environments.
While each type of gasket has its unique properties, flexible foam gasket material stands out mainly due to its combination of lightweight, excellent compressibility, and resistance to environmental factors, making it a superior option for many applications.
Choosing the Right Gasket for Your Needs
Choosing the right material involves considering various factors. First, assess the specific application and the conditions the gasket will face. Consider the temperature range, chemical exposure, and the level of compression required.
Another essential aspect to evaluate is the thickness and density of the foam material. Thicker gaskets might provide better insulation, but may also require more force to compress. It’s crucial to strike a balance that meets the application’s demands.
Lastly, don’t overlook the importance of consulting with manufacturers or suppliers to ensure you select a foam gasket that is engineered for your particular needs. This can enhance performance and ultimately save costs in the long run.
Final Thoughts
In summary, foam gasket material serves as an excellent industrial gasket solution, offering versatility, ease of installation, and exceptional sealing capabilities. With the adaptability of flexible foam gaskets, it caters to diverse industrial needs, ensuring efficiency, reliability, and optimal performance in various applications.