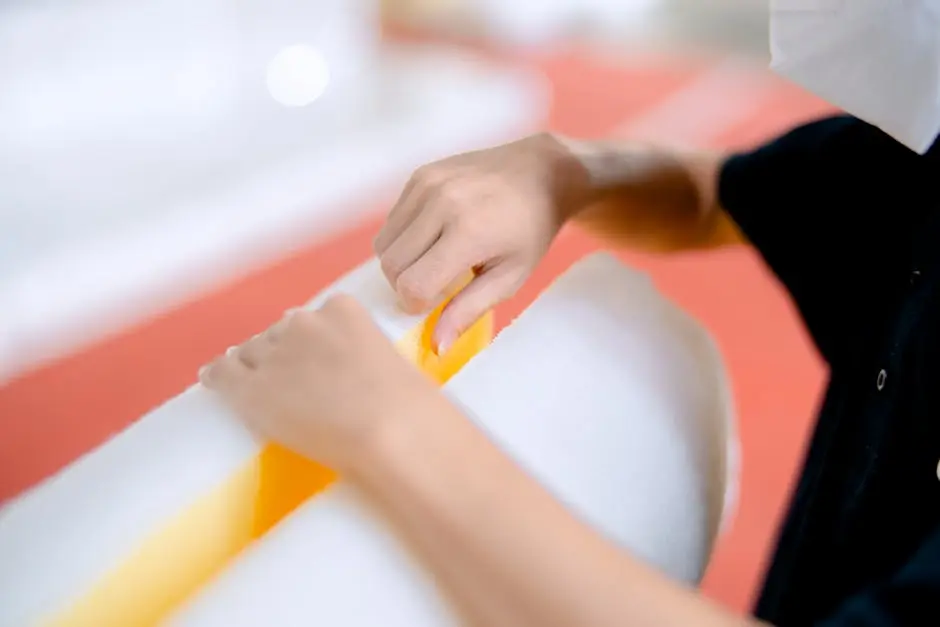
Foam die cutting is a versatile manufacturing technique that brings precision and efficiency to various industries. Understanding the applications that can benefit from this process can help businesses optimise their production and improve their product offerings.
Packaging Solutions
One of the most significant applications of foam die cutting is in packaging solutions. Businesses are continually looking for ways to ensure their products arrive safely to customers, and custom foam inserts can greatly aid in this effort.
Foam die cutting allows manufacturers to produce custom shapes and sizes that perfectly fit the product they are packaging. This not only provides cushioning but also helps to organise the product within the box, minimising movement during transit.
Additionally, the lightweight nature of foam materials ensures that shipping costs remain low. Companies looking to enhance their packaging processes can greatly benefit from the efficiency and safety by using this method.
Automotive Industry Uses
Foam die cutting plays a crucial role in the automotive industry. From sound dampening materials to insulation panels, the applications of foam cutting can significantly enhance vehicle performance.
One major use of foam die cutting in automobiles is in the creation of custom-fitted parts that minimise noise and vibration. This results in a more comfortable ride experience for passengers and contributes to the overall quality of the vehicle.
Moreover, the lightweight properties of foam can lead to overall weight reduction in vehicles, which aids in improving fuel efficiency. Manufacturers that emphasise innovation and efficiency can leverage foam die cutting to stay ahead in the competitive automotive market.
Medical Applications
In the medical field, foam die cutting provides numerous advantages. The ability to create precise and customised components is critical when developing medical devices and equipment.
For instance, foam is used in cushioning for medical devices such as wheelchairs and hospital beds. These foam strips or pads ensure comfort for patients and help prevent pressure sores.
Additionally, foam die cutting can aid in the production of protective packaging for sensitive medical instruments, guaranteeing safety during transportation. The meticulous nature of this process is aligned with the high standards required in the healthcare sector.
Consumer Products
The consumer products industry can also greatly benefit from foam die cutting. Everyday items such as electronics, toys, and appliances often require custom packaging solutions to ensure protection and aesthetic appeal.
Custom foam inserts not only safeguard products against damage but also enhance visual presentation on retail shelves. This combination of functionality and eye-catching design can create a significant competitive edge.
Furthermore, businesses can utilise this to create prototypes for product designs, allowing for quick testing and feedback. This agile approach facilitates innovation and customer satisfaction in the fast-paced consumer market.
Construction and Insulation
Foam die cutting is also prevalent in the construction industry, particularly for insulation applications. The high insulation properties of foam materials make them an efficient choice for building projects.
Custom-cut foam boards can fit seamlessly into various spaces, providing thermal insulation that helps maintain temperature regulation within a structure. This is essential in creating energy-efficient buildings that can reduce heating and cooling costs.
In addition to thermal insulation, foam die cutting can offer acoustic insulation solutions, reducing noise pollution within buildings. This multi-functional use of foam enhances both the comfort and efficiency of spaces, making it an invaluable resource in construction.
Conclusion
In summary, foam die cutting offers substantial advantages across a range of applications, from packaging to automotive and beyond. By understanding these benefits, businesses can make informed decisions about integrating this versatile manufacturing technique into their operations.