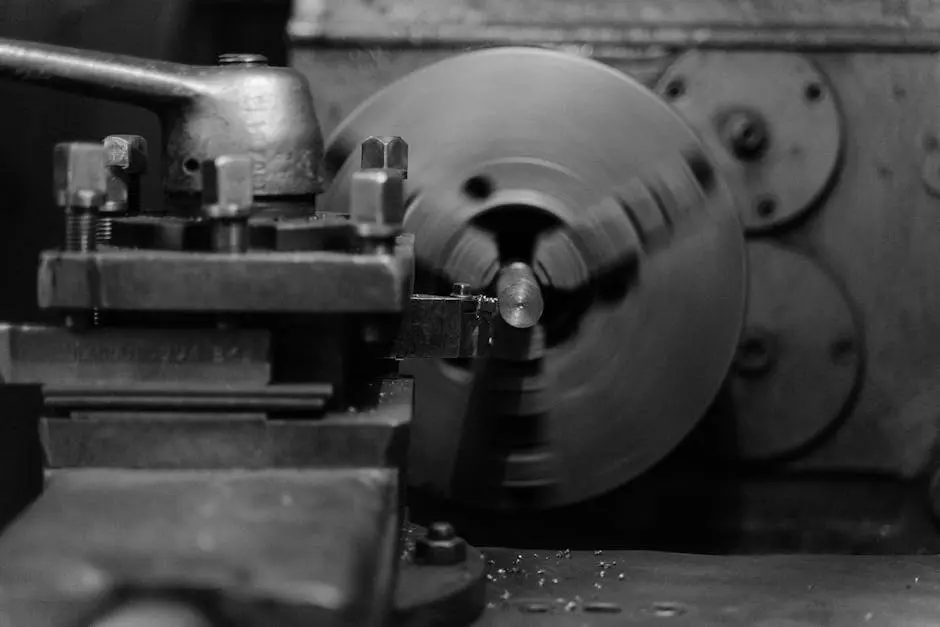
In the ever-evolving world of manufacturing, innovation plays a crucial role in enhancing efficiency and precision. One of the standout technologies making waves in recent years is foam die cutting (FDC). It’s a process that’s not only transforming how products are made but also redefining standards across various industries. Today, we’ll explore the key reasons why FDC is becoming a game-changer for manufacturers everywhere.
1. Enhancing Precision in Production
The use of foam die cutting allows manufacturers to achieve an unmatched level of precision. Through specialised dies, it creates intricate shapes with exact uniformity, essential in industries like automotive and aerospace, where even small deviations can impact functionality. This high accuracy improves product quality and builds confidence among manufacturers and end-users. Learn more about this process and our commitment to precision on our home page.
2. Reducing Material Waste Effectively
A major benefit of foam die cutting is its capability to minimise material waste. Traditional cutting methods often leave excess material, leading to higher costs and increased environmental impact. In contrast, foam die cutting’s precision enables more efficient material layouts, reducing scrap and supporting sustainability efforts. Discover how our foam products align with waste reduction goals.
3. Improving Design Flexibility with Foam Die Cutting
FDC provides unique flexibility in design, allowing for creative exploration without needing costly new molds. This adaptability accelerates prototype development, enabling companies to swiftly respond to emerging trends. This flexibility is ideal for businesses seeking innovation and efficiency, as detailed on our about us page.
4. Increasing Production Speed
Speed is a critical factor in manufacturing, and FDC enhances production efficiency by reducing setup time. The process enables quick shifts between designs, expediting production cycles while maintaining high quality. This streamlined approach is a valuable advantage in meeting tight deadlines.
5. Lowering Operational Costs with Foam Die Cutting
Combining efficiency, waste reduction, and speed leads to lower operational costs with foam die cutting. Companies benefit from optimised material use and minimised labor and overhead expenses, which enhances cost-effectiveness. These savings allow reinvestment in areas like product innovation, as showcased in our range of foam products.
6. Facilitating Customisation and Personalisation
Today’s consumers value personalised products, and foam die cutting easily supports customisation. This process allows manufacturers to adjust designs quickly to meet specific customer needs, which helps businesses stand out in competitive markets. Our commitment to customisable solutions is detailed on our about us page.
7. Supporting Sustainable Manufacturing Practices
Foam die cutting aligns with sustainable practices by reducing waste and optimising resource use. Many foam materials used in production are recyclable, supporting eco-friendly initiatives while still meeting high production demands. Learn more about our sustainable approach on our home page.
8. Streamlining the Prototyping Process with Foam Die Cutting
Prototyping can be time-consuming, but foam die cutting streamlines this phase with quick tooling and fast turnarounds. This efficiency allows manufacturers to test and refine designs before full production, which helps reduce costs and expedite product launches.
9. Expanding Applications Across Industries
FDC serves many sectors, including automotive, medical, and packaging, providing precision and durability in various applications. This versatility appeals to manufacturers across multiple industries. Explore how our foam products can meet diverse industry needs.
10. Enhancing Safety in the Workplace
Safety is paramount in manufacturing, and foam die cutting enhances workplace safety by reducing the risks associated with manual cutting methods. The controlled process minimises potential accidents, promoting a safer environment for employees.
11. Boosting Collaboration Between Teams with Foam Die Cutting
FDC encourages collaboration across design, engineering, and production teams, enhancing workflow and efficiency. This collaboration supports quick iterations, helping team members streamline processes and create better products. Learn more about our collaborative approach on our about us page.
12. Elevating Product Quality and Consistency
The precision of FDC ensures product quality and consistency, reducing variations and defects. This method allows companies to uphold high standards and build trust with their customers, essential for strong brand reputation.
13. Simplifying the Supply Chain
Foam die cutting supports a simpler supply chain by maximising efficiency and reducing waste, which creates a more seamless flow from production to distribution. This adaptability strengthens supply chain resilience, crucial in today’s fast-paced market.
14. Adapting to Market Trends Quickly with Foam Die Cutting
FDC allows manufacturers to respond rapidly to new market trends and customer preferences. The quick adjustments and prototyping capabilities help businesses adapt efficiently, essential for staying competitive in a dynamic market.
15. Harnessing Advanced Technologies
FDC leverages advanced technologies like CAD and automated systems, which enhance precision and efficiency. These innovations ensure our production processes stay at the forefront of industry advancements, as detailed on our home page.
Foam die cutting offers comprehensive advantages, positioning manufacturers competitively by improving precision, sustainability, and adaptability.